
A SIPOC structure helps the process owner and those working on the process to clarify the primary elements of a process and agree on on the boundaries of what they will be working on. With this tool, we build our first organized view of the work process and set the foundation for applying the breakthrough DMAIC strategy. It is a vital supplementary component to a process map. Those diagrams are also referred to as high-level process maps because they do not contain much detail. It is a visual tool for documenting a business process from the beginning to the end. In this figure, you can see an example of the format of a SIPOC diagram.
#Process modeling tools sipoc free#
Let’s have a look at the SIPOC diagram in more detail.Īttend our 100% Online & Self-Paced Free Six Sigma Training. It helps clearly understand the purpose and the scope of a process. Inputs come from suppliers, and the outputs go to customers.
#Process modeling tools sipoc series#
The SIPOC diagram is fairly common among business process experts as a logical way of looking at a process in terms of a series of steps that converts an input into an output. In Lean Six Sigma Green Belt course, and even in free Lean Six Sigma course, you will learn that it is an acronym that stands for Suppliers, Inputs, Process, Outputs, and Customers. For the whole process to work and bring favorable business, all elements in SIPOC should be aligned and supports the ultimate goal of the business.In a Six Sigma project, the SIPOC diagram is one of the important tools in the Six Sigma DEFINE phase of the DMAIC framework. Again, input requirements must be followed. Lastly, determine the suppliers that can provide you the necessary inputs. After establishing the process, the next things to think about are the inputs, or the things that you will need for the process to be executed. Bear in mind the requirements of the output should be a major consideration when designing the process. When you already have a product in mind, the next step is to create a process that will generate that product. Upon reaching a clear idea of the target customers’ needs, you derive a product to address the needs. You will start from the “customers” by getting the VOC (voice of the customer) through surveys and interviews or by simply projecting needs through feasibility studies. This is common when putting up a new business or creating a new line of business within an established one.
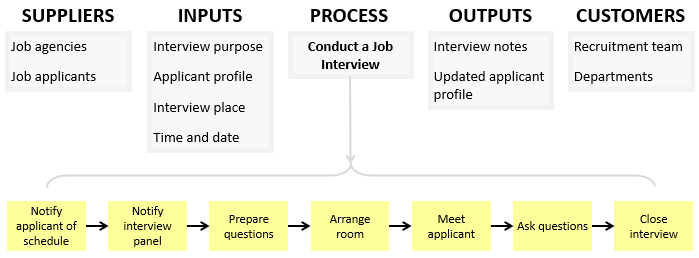
When creating a new process, planners usually follow the COPIS (reversed SIPOC) model.

From the analysis, managers will have a clearer idea of whether to streamline on expenses or infuse more resources to improve the efficiency of the process. SIPOC will help process auditors to determine if the process is still working for the business. It is not unusual to employ SIPOC on established processes if there’s a low turnout on sales or output or if the expense ration against income is high. In case of misalignment, go back to your process. Your customers’ feedback or your projected customers’ needs should be addressed by your output.
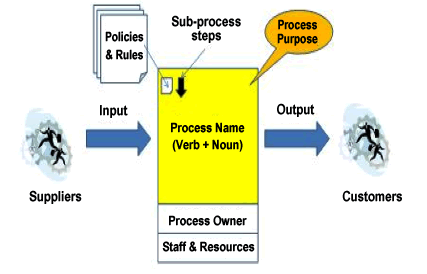
